OUR CAPABILITIES
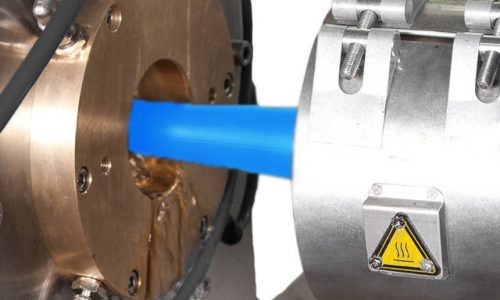
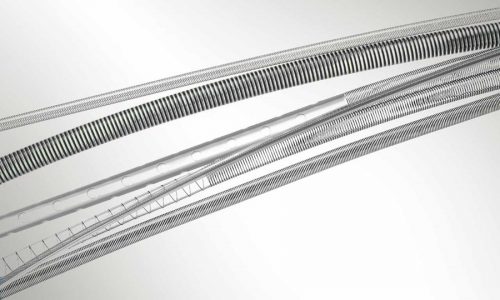
EXTRUSION
Precise, quality and remarkable are the words to describe CCB’s medical tube extrusion capability which allows us to produce a number of medical devices for our German partner VBM Medizintechnik GmbH and other international companies.
We are specialized in flexible or rigid tubing with a broad range of single and multi-lumen profiles to suit your needs and are capable to control the quality based on your requirements. Our 24/7 operation located in a controlled area is capable of meeting your production needs.
CCB also specialises in ultra-thin reinforced medical tubing whereby a tube is coiled with a metal or non-metallic spring to provide unparallel fexibility, kink-resistance and toughness while providing a soft comfortable feeling products for the benefit of the end-users.
We are capable of extruding tubings with different characteristics of varied geometries, utilising materials ranging from medical PVC to thermoplastic to even medical silicone extrusion. Our in-house construction of customized extrusion tooling is great to produce your required tubing profiles. We also provide process validation with appropriate documentation. If you’re looking for an extrusion partner, look no further.
BLOW MOULDING
CCB is equipped with multiple years of experience in blow moulding capabilities, specialising in both extrude-blow and inject-blow technologies. For the extrude-blow technology, we could blow soft, flexible Polyvinyl Chloride (PVC), Polyurethane (PU) and Thermoplastic Elastomers (TPE) into medical balloons in a wide range of profiles and comply with the change in market trends by utilising DEHP-free compounds. We also offer single and dual-arm technology solutions based on your project volume and required efficiency.
CCB also offers bottle forming solutions for your medical bottle or container projects. We provide different solutions such as single-step extrude-blow or two-step inject-blow bottle forming technologies based on the material behaviours and annual consumption requirements. We have extensive expertise in various materials such as Polypropylene (PP), Polyethylene (LDPE or HDPE), Polyethylene Terephthalate (PET), and Acrylonitrile Butadiene Styrene (ABS).
Our decades of experience, in-house capability, tooling and know-how allow us to fabricate your blow-moulding products to your specifications with consistency and precision. Using medical-grade materials and processing in highly controlled operation areas, we strive to ensure the end products are free of contaminants. We also provide process validation with appropriate documentation and our 24/7 operation located in a controlled area is capable of meeting your production needs.
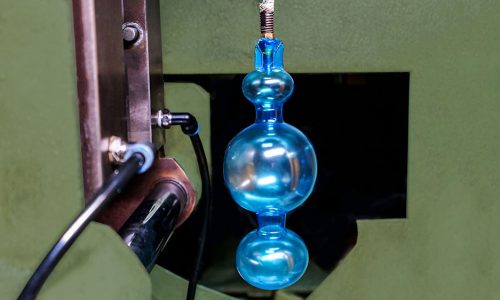
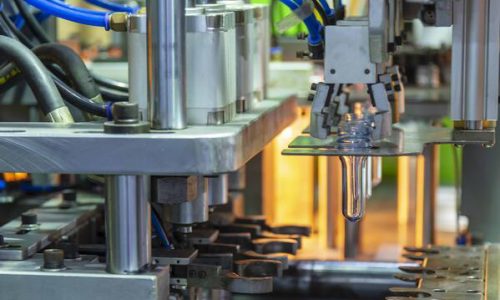
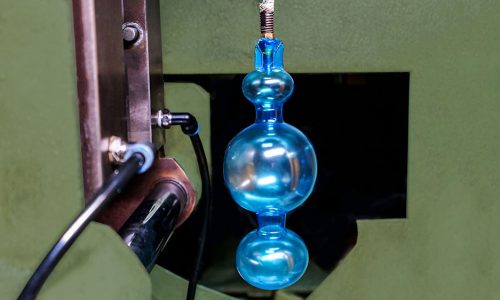
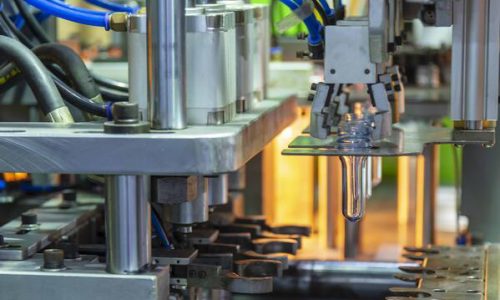
BLOW MOULDING
CCB is equipped with multiple years of experience in blow moulding capabilities, specialising in both extrude-blow and inject-blow technologies. For the extrude-blow technology, we could blow soft, flexible Polyvinyl Chloride (PVC), Polyurethane (PU) and Thermoplastic Elastomers (TPE) into medical balloons in a wide range of profiles and comply with the change in market trends by utilising DEHP-free compounds. We also offer single and dual-arm technology solutions based on your project volume and required efficiency.
CCB also offers bottle forming solutions for your medical bottle or container projects. We provide different solutions such as single-step extrude-blow or two-step inject-blow bottle forming technologies based on the material behaviours and annual consumption requirements. We have extensive expertise in various materials such as Polypropylene (PP), Polyethylene (LDPE or HDPE), Polyethylene Terephthalate (PET), and Acrylonitrile Butadiene Styrene (ABS).
Our decades of experience, in-house capability, tooling and know-how allow us to fabricate your blow-moulding products to your specifications with consistency and precision. Using medical-grade materials and processing in highly controlled operation areas, we strive to ensure the end products are free of contaminants. We also provide process validation with appropriate documentation and our 24/7 operation located in a controlled area is capable of meeting your production needs.
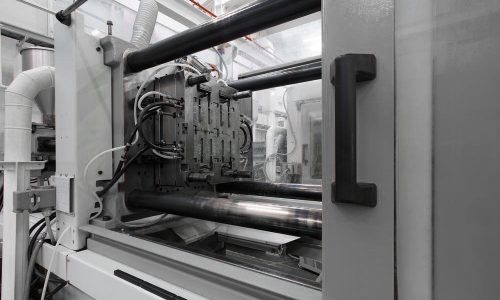
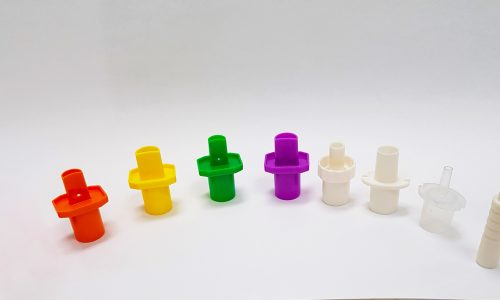
INJECTION MOULDING
With decades of technical know-how and a team of experienced engineers, CCB is capable to develop your customized mould and the injection process. Does your product require a cold or hot runner system? How many cavities? How is the ejecting mechanism? We have all the answers here at CCB.
CCB is capable of moulding various medical parts and have worked with different polymers, even PVC injections. We have both horizontal and vertical machines, allowing flexibility and complex tooling design for your product needs. We also offer over-moulding technologies, boosted by our knowledge of materials. CCB also has silicone compression moulding capability to produce quality silicone products using medical-grade silicone which offers great chemical, heat, mechanical and electrical properties.
We strive to improve on the process to ensure the injected parts are of the best possible quality. Our in-house tooling department also offers consistent mould maintenance and quick repair. We also provide process validation with appropriate documentation. Our 24/7 operation located in a controlled area is capable of meeting your production needs.
MEDICAL PACKAGING
Sterilized medical devices are a crucial part of our healthcare system. A sterile barrier system effectively keeps the finished product under sterile conditions and prevents sterilized parts from being contaminated. This ensures the integrity of the device remains uncompromised and the safety of the end patient during medical procedures.
There are many aspects that require detailed designs, testing capabilities, and technical know-how to produce a consistent medical packaging line. We can assist in developing packaging tooling and have experience in various types of Medical paper, Tyvek peel/tear pouches, state-of-the-art formed pouches, blister pack technology, Hawo sealing, and our multiple cleanroom setups with tight environmental control are capable of solving your packaging requirements, thus protecting the integrity of the medical devices.
We can assist in individual printing and labelling on primary packagings such as bar codes, QR codes, and pictograms according to international standards. Our in-house toolmaker could customize the form-fill-seal tools for the packaging machines based on your requirements. We also carried out packaging process validation with appropriate documentation. Consult us on this often overlooked yet crucial step of your production today!
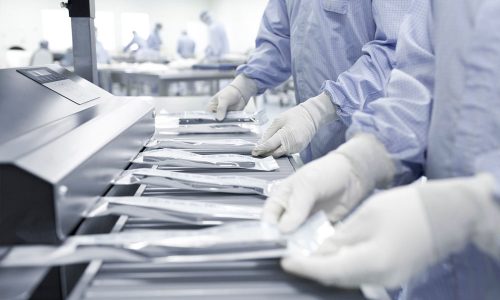
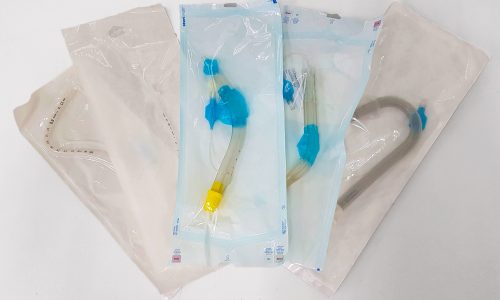
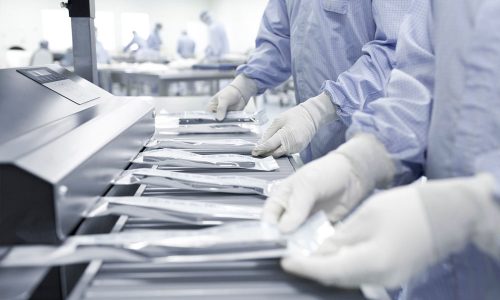
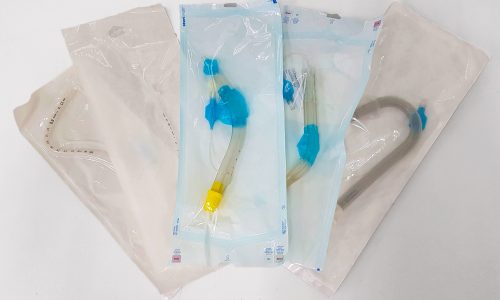
MEDICAL PACKAGING
Sterilized medical devices are a crucial part of our healthcare system. A sterile barrier system effectively keeps the finished product under sterile conditions and prevents sterilized parts from being contaminated. This ensures the integrity of the device remains uncompromised and the safety of the end patient during medical procedures.
There are many aspects that require detailed designs, testing capabilities, and technical know-how to produce a consistent medical packaging line. We can assist in developing packaging tooling and have experience in various types of Medical paper, Tyvek peel/tear pouches, state-of-the-art formed pouches, blister pack technology, Hawo sealing, and our multiple cleanroom setups with tight environmental control are capable of solving your packaging requirements, thus protecting the integrity of the medical devices.
We can assist in individual printing and labelling on primary packagings such as bar codes, QR codes, and pictograms according to international standards. Our in-house toolmaker could customize the form-fill-seal tools for the packaging machines based on your requirements. We also carried out packaging process validation with appropriate documentation. Consult us on this often overlooked yet crucial step of your production today!
ASSEMBLY & SECONDARY OPERATION
CCB is the one-stop solution centre for your product development and commercialization needs. As a reliable partner for mass manufacturing, we offer a wide range of secondary, value-adding operations to add the finishing touches to your medical devices. Our 24/7 operation located in controlled areas or cleanrooms is capable of performing any secondary operations based on your product specifications. Our certified cleanrooms are under controlled environmental particles and monitored microbiologically.
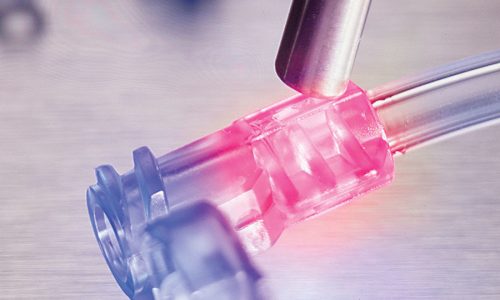
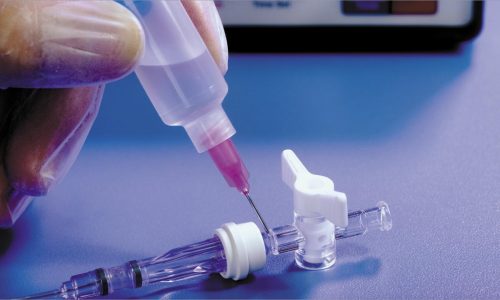
BONDING
Here at CCB, we offer medical UV adhesives and solvent bonding solutions that suit your product requirements. Bonding between a range of substrates requires the consideration of various factors, such as the sterilisation process, as it will have an impact on the strength of post-cured glue. Whether it is USP Class VI standards and medical grade adhesives, or the consideration of sterilisation compatibilities such as gamma and ETO, we are experienced in giving you the best advice for your bonding needs. Apart from traditional bonding solutions, CCB also offers ultrasonic welding process. Fast, precise and consistent, the ultrasonic waves can hit a specific location on the plastic, creating bonds that do not alter the strength of the plastic around the joint as it was done without any heat source.
PRINTING
Printing needs are growing with the rise of proper labelling on medical products. Here at CCB, we have decades of experience in a wide range of printing services. Be it indicator marking, logo, numerical characters or hard-to-print low energy surfaces, we do it all. We utilise different ink materials of different colours, made from biocompatible sources to ensure product safety. Our state-of-the-art surface pre-treatment technology can impart changes on the printing surfaces, guaranteeing a high adhesion, high quality and scratch-resistant print even on materials with low surface energy, such as Polyethylene (PE), Polypropylene (PP), and Teflon.
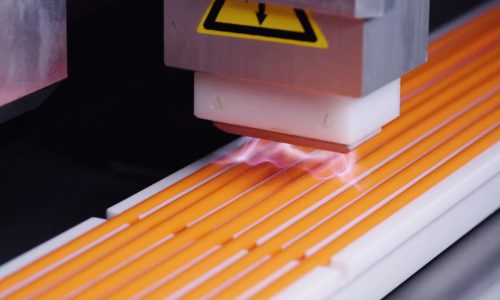
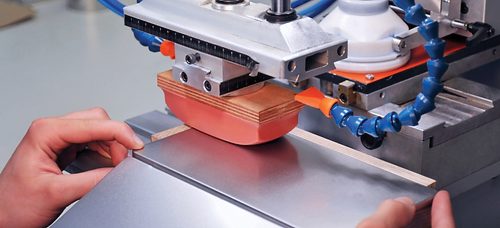
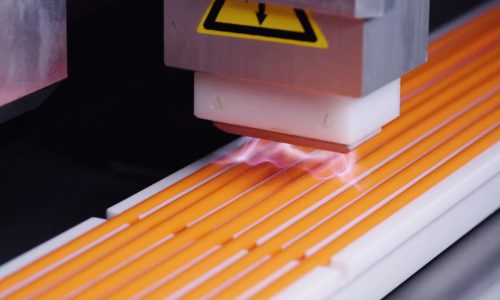
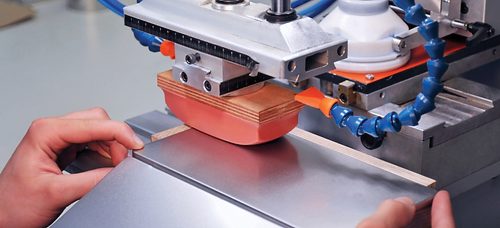
PRINTING
Printing needs are growing with the rise of proper labelling on medical products. Here at CCB, we have decades of experience in a wide range of printing services. Be it indicator marking, logo, numerical characters or hard-to-print low energy surfaces, we do it all. We utilise different ink materials of different colours, made from biocompatible sources to ensure product safety. Our state-of-the-art surface pre-treatment technology can impart changes on the printing surfaces, guaranteeing a high adhesion, high quality and scratch-resistant print even on materials with low surface energy, such as Polyethylene (PE), Polypropylene (PP), and Teflon.
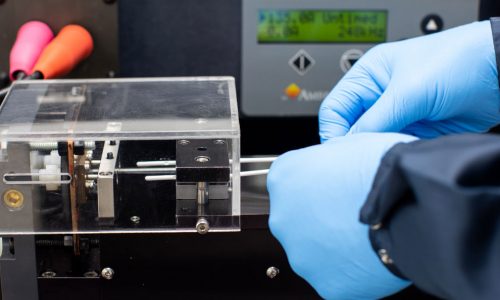
TIP FORMING
Sharp edges are undesirable for medical insertion devices such as catheters, airway and drug delivery tubes. Our unique tip forming process is capable of creating any tip geometries, tapered diameters, thickness, rounded ends without any sharp edges, or whether it is an open-end or close-end tip forming. Our in-house machining department can produce customized tip forming equipment and the construction of circular welding machines for your personalized solutions. These custom-made pots are easy to use, swift cycle time, and can be made for a wide range of sizes and materials.
SMOOTH-EDGED HOLE PUNCHING
Many medical devices require intricate machining techniques to produce the holes on catheters, airway and drug delivery tubes for medical procedures. This is where CCB’s smooth-edged hole punching technology comes in. We have our own custom-built, in-house hole punching facility to provide customers with a wide range of solutions from multiple holes to different sizes or geometries. Our precise solutions using our custom-made machines are unrivalled and are capable of delivering the quality you desired.
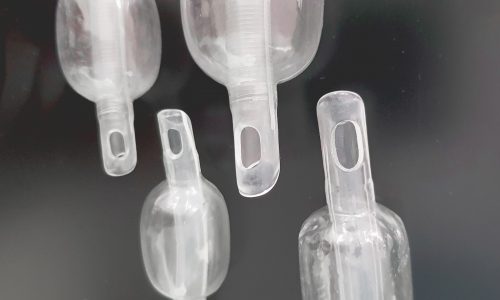
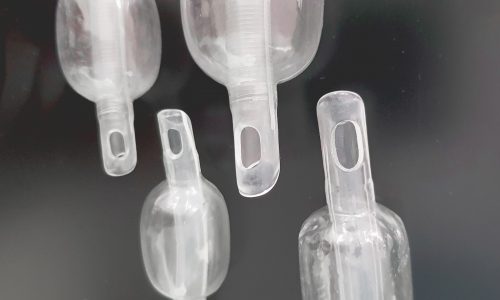
SMOOTH-EDGED HOLE PUNCHING
Many medical devices require intricate machining techniques to produce the holes on catheters, airway and drug delivery tubes for medical procedures. This is where CCB’s smooth-edged hole punching technology comes in. We have our own custom-built, in-house hole punching facility to provide customers with a wide range of solutions from multiple holes to different sizes or geometries. Our precise solutions using our custom-made machines are unrivalled and are capable of delivering the quality you desired.
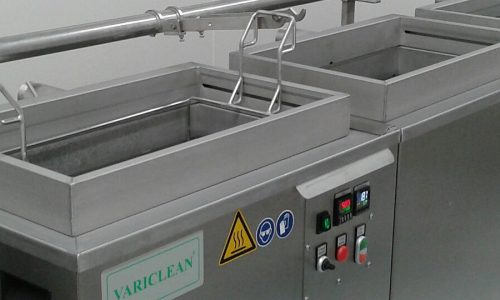
CLEANING
Cleanliness is paramount for medical devices. Here at CCB, we use high-frequency, high-intensity ultrasonic waves to clean hard-to-reach crevices. Our state-of-the-art ultrasonic cleaning systems essentially remove foreign particles, grease, and other contaminants without any human touch. This automated cleaning process is safe, effective and quick to ensure your medical device is cleaned along with our comprehensive documentation and reports. After all, at CCB Medical Devices, the highest priority is product quality.